Environmentally Friendly Durable Plastic O-PVC Pipe Making Extrusion Line
Impact-resistant, Low-temperature-resistant, Strong-toughness PVC-O Pipe Manufacturing Line
Aceextech machines performance reached the international first-class level, and all indicators passed the inspection of the National Chemical Building Material Testing Center. We already successfuly provided multiple PVC-O pipe production lines for many companies and scientific research institutions at home and abroad. We can provide customers with a complete set of technical solutions such as equipment, processes, formulas, and personnel training, as well as turnkey projects.
PVC-O Plastic Pipe Making Extrusion Line
The PVC-O pipe is a pipe produced by the bidirectional stretching process. The perfomance of the pipe producedby this proces is greatly improved compared with PVC-U pipe, the impact resistance of the pipe isimproved by about 4 times, the toughness is still maintained at minus -20" C, and the wall thickness ofPVC-U pipe is reduced by half under thesame pressure. About 47% of the raw material is saved, and athinner wall thickness means that the pipes water conveying capacity is stronger, the pipes are lighterand more convenient to install, and the transportation cost is lower.
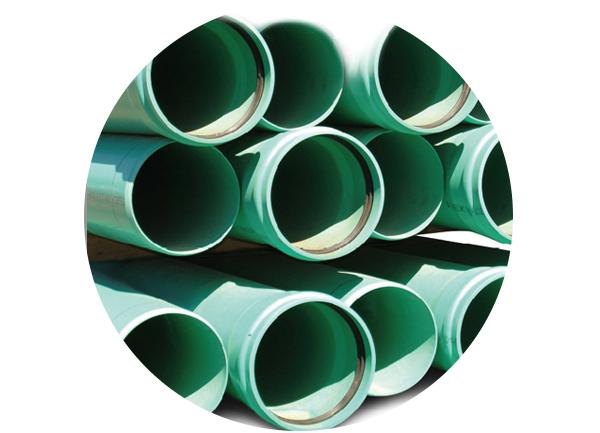
PVC-O Pipe Introduction
By stretching the PVC-U pipe produced by extrusion in both axial and radial directions, the long PVC molecular chains in the pipe are arranged in an orderly biaxial direction, so that the strength, toughness and resistance of the PVC pipe can be improved. The performance of punching, fatigue resistance, and low temperature resistance has been greatly improved. The performance of the new pipe material (PVC-O) obtained by this process greatly exceeds that of the ordinary PVC-U pipe.
Studies have shown that compared with PVC-U pipes, PVC-O pipes can greatly save raw material resources, reduce costs, improve the overall performance of the pipes, and lower the cost of pipe construction and installation.
OPVC Pipe Features
Relevant Standards for PVC-O Pipes
International Standard: ISO 16422-2014 South African Standard: SANS 1808-85:2004
Spanish standard: UNE ISO 16422 American standard: ANSI/AWWA C909-02
French Standard: NF T 54-948:2003 Canadian Standard: CSA B137.3.1-09
Brazilian Standard: ABTN NBR 15750 Indian Standard: IS 16647:2017
China Urban Construction Standard: CJ/T 445-2014 (GB national standard is being drafted)
PVC-O Pipe Production Method
Technical Parameters
Diameter (mm) |
Pressure (bar) |
Thickness (mm) | Linear weight (kg/m) | Stretching ratio (%) | Standard | Speed Pro | ||
Capacity Kg/h | Speed (m/h) | Capacity Kg/h | Speed (m/h) | |||||
90 |
1.25 | 1.7 | 0.67 | 1.89 | 90 | 134 | 145 | 215 |
16 | 2.1 | 0.82 | 1.89 | 90 | 109 | 160 | 198 | |
20 | 2.6 | 1.01 | 1.84 | 90 | 89 | 160 | 160 | |
110 | 12.5 | 2 | 0.96 | 1.96 | 140 | 145 | 220 | 225 |
16 | 2.6 | 1.25 | 1.92 | 140 | 111 | 220 | 188 | |
20 | 3.2 | 1.52 | 1.92 | 140 | 91 | 220 | 166 | |
25 | 4 | 1.89 | 1.86 | 140 | 73 | 220 | 134 | |
160 | 12.5 | 2.9 | 2.03 | 1.95 | 170 | 83 | 410 | 199 |
16 | 3.7 | 2.58 | 1.95 | 170 | 66 | 150 | 175 | |
20 | 4.6 | 3.19 | 1.92 | 170 | 54 | 500 | 155 | |
25 | 5.8 | 3.99 | 1.86 | 170 | 43 | 500 | 125 | |
200 | 12.5 | 3.6 | 3.15 | 1.95 | 220 | 68 | 540 | 171 |
16 | 4.6 | 4.01 | 1.94 | 220 | 55 | 540 | 135 | |
20 | 5.7 | 4.94 | 1.91 | 220 | 44 | 540 | 109 | |
25 | 7.2 | 6.19 | 1.86 | 220 | 35 | 540 | 87 | |
250 | 12.5 | 4.5 | 4.93 | 1.95 | 240 | 48 | 190 | 119 |
16 | 5.8 | 6.32 | 1.94 | 240 | 37 | 190 | 93 | |
20 | 7.2 | 7.80 | 1.89 | 240 | 30 | 190 | 75 | |
25 | 9 | 9.68 | 1.86 | 240 | 24 | 190 | 60 | |
315 | 12.5 | 5.7 | 7.86 | 1.95 | 295 | 37 | 630 | 80 |
16 | 7.2 | 9.89 | 1.95 | 295 | 29 | 630 | 64 | |
20 | 9 | 12.29 | 1.90 | 295 | 24 | 630 | 51 | |
25 | 11.4 | 15.44 | 1.85 | 295 | 19 | 630 | 40 | |
400 | 12.5 | 7.2 | 12.62 | 1.95 | 410 | 32 | 720 | 56 |
16 | 9.2 | 16.04 | 1.93 | 410 | 25 | 720 | 45 | |
20 | 11.4 | 19.76 | 1.89 | 410 | 21 | 720 | 36 | |
25 | 14.4 | 24.77 | 1.86 | 410 | 16 | 720 | 28 |
Main Extruder
The main extruder features an advanced parallel twin screw design that ensures stable material feeding and highly efficient plasticizing performance. The 38:1 L/D ratio enhances the melting capability, making it ideal for HDPE pipe, sheet, and profile production. Equipped with a high-torque gearbox and energy-saving motor, it operates smoothly with low noise and reduced energy consumption.
Equipped with advanced temperature control systems, the extruder maintains stable quality across varying production conditions, accommodating different formulations.
Mould
The mould incorporates a specially designed flow channel that ensures uniform material distribution and optimized melt flow, suitable for producing HDPE pipes of various diameters and wall thicknesses. The die head is precision-machined and features a chrome-plated surface for enhanced wear resistance and corrosion durability, ensuring a long service life.
Durability: Molds are made from high-quality alloys, offering longer service life and the ability to withstand high temperatures and pressures.
Vacuum Calibration Tank
The vacuum tank is equipped with an efficient vacuum calibration system to ensure rapid pipe forming and precise dimensions. Constructed from stainless steel, it offers excellent corrosion resistance. The tank features automatic water level control and a water circulation system, significantly saving water resources and reducing energy consumption.The spray cooling tank uses multiple high-efficiency spray nozzles for uniform cooling, quickly lowering pipe temperature and ensuring that the finished product maintains its shape. A water temperature control system is integrated to further enhance production stability and product quality.
Haul-off Unit
The haul-off unit is designed with pneumatic pressure and features a maximum traction force of 35,000N, ensuring stable and reliable performance during extrusion processes. The unit's traction speed is adjustable up to 4m/min, allowing for precise control. Equipped with a high-grade silicone rubber block (55x29x28mm) with a high friction coefficient, the system offers long-lasting, efficient traction while minimizing wear.
Infrared Heating Machine
Infrared heating machine is mainly used to heat and preheat OPVC materials. Through radiation heating, OPVC materials can be quickly heated to a temperature suitable for extrusion, reducing the heating burden of the extruder and ensuring its temperature is uniform and stable, thereby improving production efficiency, reducing internal stress, bubbles and other defects in the pipe, improving the physical properties and surface quality of the pipe, and reducing energy consumption and equipment loss.
CalibrationTank
The CalibrationTank uses water cooling to prevent deformation, allowing the extruded high-temperature soft pipe to quickly cool and shape, ensuring that the outer diameter, roundness and wall thickness of the pipe are uniform and consistent, meeting the design standards, improving the surface finish, and ensuring the dimensional accuracy, shape stability and surface quality of the pipe. It is an indispensable key equipment in the extrusion production line.
Cutting Machine
The cutting machine features a high-precision synchronous control system, ensuring dust-free cutting with smooth and clean edges. The blade rotates around the pipe and is pneumatically controlled for precise entry, allowing for high-quality cuts without any debris. The cutting speed is synchronized with the production line at up to 4m/min, optimizing both production efficiency and quality. The machine is controlled by Siemens PLC, ensuring stable and reliable performance. Additionally, the soundless cutting chamber reduces noise pollution during operation.