Feeding System
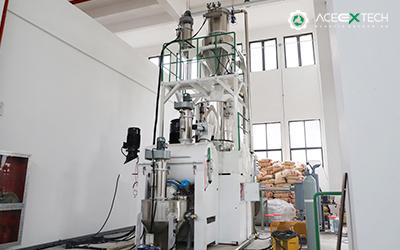
* Raw Material Conveyor: Transports PET resin, regrind material, color masterbatch, etc., from storage bins to the extruder.
* Multi-component Feeding System: Precisely controls the ratio of virgin material, regrind, color masterbatch, etc., ensuring uniform mixing.
Extruder

The extruder, typically a single-screw or twin-screw type, melts the PET material by heating and extrudes it through the die head into a thin sheet. Twin-screw extruders are better suited for processing PET, providing higher mixing efficiency and reducing viscosity drop.
Die Head
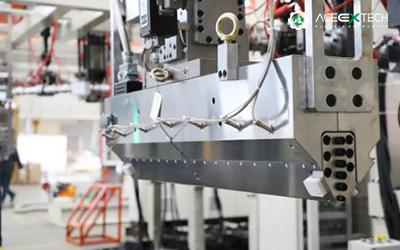
The die head is the component that evenly extrudes the molten PET into a sheet form. The design of the die head is crucial in achieving uniform sheet thickness.
Cooling System
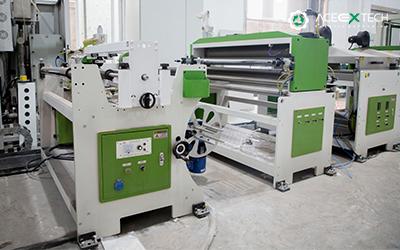
* Cooling Rolls: These rolls are used to cool the extruded PET sheet. Symmetric thin-wall cooling rollers are often used to improve cooling efficiency and production capacity.
* Air Cooling System: Some lines are equipped with an air cooling system to further control the temperature of the sheet.
Calendering/Traction System
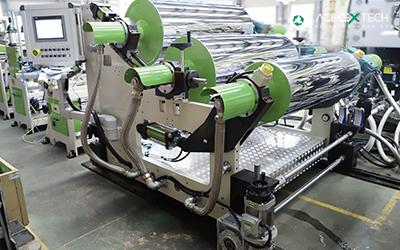
The calendering rollers help pull the cooled PET sheet through at the right speed, ensuring its uniformity and stretching it to the desired width.
Cutting System
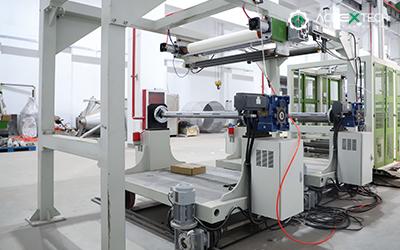
Slitting Machine/Shearing Machine: The cooled PET sheets are cut into the desired sizes using slitting machines (to cut the sheet width) and shearing machines (to cut the length).
The cutting system can adjust the sheet size to meet product specifications.
Winding Device
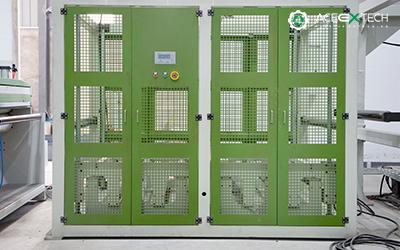
* The cut PET sheets are wound into rolls for easy handling and packaging.
* The winding system ensures that the sheets are wound without wrinkles or deformation.
Automation Control System
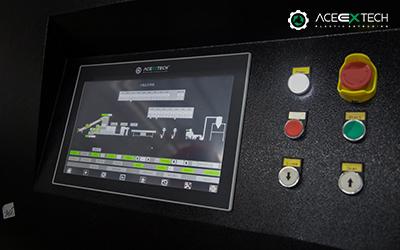
This includes temperature control, speed control, pressure control, etc., to monitor the production process in real-time, ensuring stable production and high-quality sheets.