Material Handling System
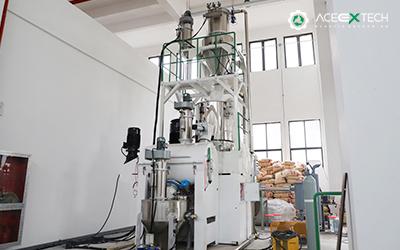
To mix the virgin material and the recycle flakes.
Single Screw Extruder
Screw: The screw conveys the granules along the barrel, melting them and turning them into a uniform molten mass.
Screw adopts special mixing function and high plasticizing ability design to ensure good plasticizing of plastics stable high yield extrusion;
Heating Zone: The material is heated in this section using electrical heating systems to reach the required extrusion temperature, typically ranging from 200°C to 280°C.
Cooling Zone: In this area, the molten polypropylene is cooled to maintain its flow characteristics and stability.
Special Screen Changer
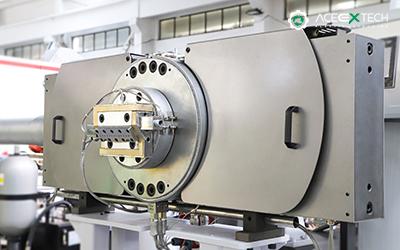
Long considered the workhorse of polymer melt filtration, Hydraulic Slide Plate Screen Changers (HSC) are an efficient, economic filtration solution for film, sheet, pelletizing and a host of other applications able to tolerate a momentary process disruption. The design uses a two-position reciprocating slide plate to rapidly move screen packs in and out of the melt stream ‘on-the-fly’.
Melt Pump
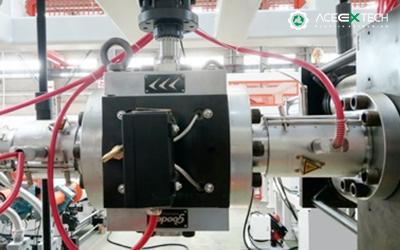
It is an essential component in many plastic extrusion and molding processes, particularly when handling high-viscosity materials such as molten polymers. It is used to provide a consistent, controlled flow of the molten material through the extrusion system, helping to improve product quality and manufacturing efficiency.
T-Die
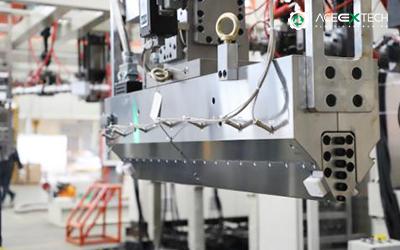
The die head is used to shape the molten polypropylene into a uniform sheet. It is designed to provide a specific width and thickness distribution for the sheet. The die head is usually equipped with a temperature control system to maintain consistent extrusion temperatures and prevent material degradation.
Hanger die head adopts special double throttle design, which makes the thickness adjustment of the plate more accurate. Selectable with a variety of forms of hydraulic one-way net changer or double-way net changer; And non-stop double channel change network. Through efficient static mixer, melt output metering pump, to ensure that the material level stable extrusion;
Three-roll Calender
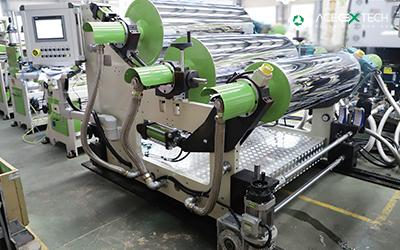
The three-roller calendering machine offers significant advantages in terms of precision, efficiency, and versatility. It is particularly well-suited for producing high-quality plastic sheets and films with uniform thickness, smooth surfaces, and customizable textures. These benefits make it a popular choice in a variety of industries, including packaging, automotive, and textiles.
Three roller calender adopts horizontal vertical or 45° inclined type. Adjustable lifting mode gap convenient adjustment to ensure the calender effect;
Temp. Controller
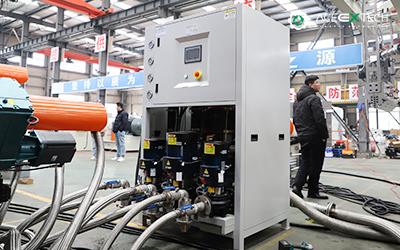
The system features a combined independent roller temperature control system, which effectively and accurately controls the temperature, ensuring uniform thickness. The winding machine is equipped with a high-torque motor, allowing for adjustable speed and tension. Through slitting and automatic speed detection, the equipment can accurately set the required product width and length.
Edge Trimming Unit
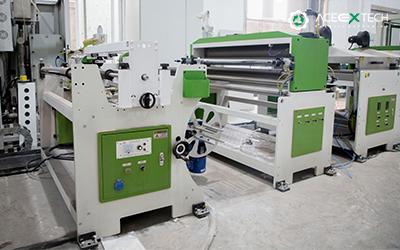
Edge trimming unit
The cutter or slitter is used to cut the extruded PP sheet into the desired lengths or widths. There are two common types of cutting:
* Fixed-length Cutting: The sheet is cut into predetermined lengths based on customer requirements.
* Slitting: The sheet is cut into multiple narrower sheets or strips, depending on the product specifications.
Edge trimming winder
The winding machine is used to roll the continuous PP sheet into rolls for easy storage and transportation. The machine is equipped with an automatic tension control system to ensure that the sheets are wound with the correct tightness, preventing damage or deformation.
Conveyor:Transportation of sheets to the Haul-off
Haul-off
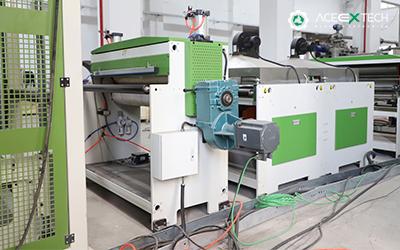
The haul-off unit continuously pulls the cooled sheet at a precise speed to prevent stretching or uneven thickness. It ensures that the sheet moves at the correct rate to match the extrusion speed, preventing deformations.
Winder
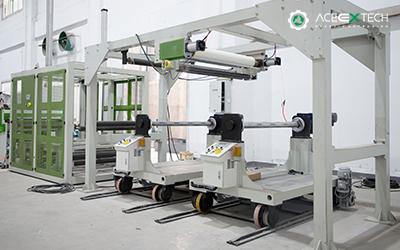
The winding machine is used to roll the continuous PP sheet into rolls for easy storage and transportation. The machine is equipped with an automatic tension control system to ensure that the sheets are wound with the correct tightness, preventing damage or deformation.